“And I don’t know what kinda ropes…”
Chances are, Taylor Swift wasn’t musing about the wire ropes stabilizing the stage she was performing on that particular night when she belted out “Wait for Me.” Fortunately, those wire ropes were anchored from the stage roof to ballast at the base below the stage.
All temporary roof systems are anchored in some manner to the ground so that they can remain upright when the wind blows. Whether that’s a trailer, heavy scaffold, permanent earth anchors, or ballast, the anchorage has to be adjustable, and strong enough to resist forces from powerful winds.
What is ballast?
Think about the last time you played basketball on a cul-de-sac hoop, or sat under a backyard umbrella. Now, think about the last time that backyard umbrella lifted out of its base or toppled. The water or sand in the base of the hoop, or sand bags at the base of the umbrella is ballast. Simply, ballast is something heavy that anchors and provides stability for something else. Besides water or sand, the best temporary option is concrete. All of these methods are removable and are used to hold down the element from overturning or sliding.
In a temporary roof system (the structure you see at most outdoor pop-up concerts), forces from winds want to push the structure or overturn it. When the system is erected in a park or field, permanent anchorage solutions, like permanent ground anchors or foundations, are not cost effective. Temporary ballast is used instead to prevent sliding and overturning. Taut wire ropes connect the ballast to the temporary structure; the force in the wire rope is resisted by the weight of the concrete blocks. In many of our designs, wire ropes are oriented at a 45 degree angle. The tension in the wire rope can be broken down into two components: vertical and horizontal. The steeper the degree in the wire rope, the more uplift (vertical) on the base.
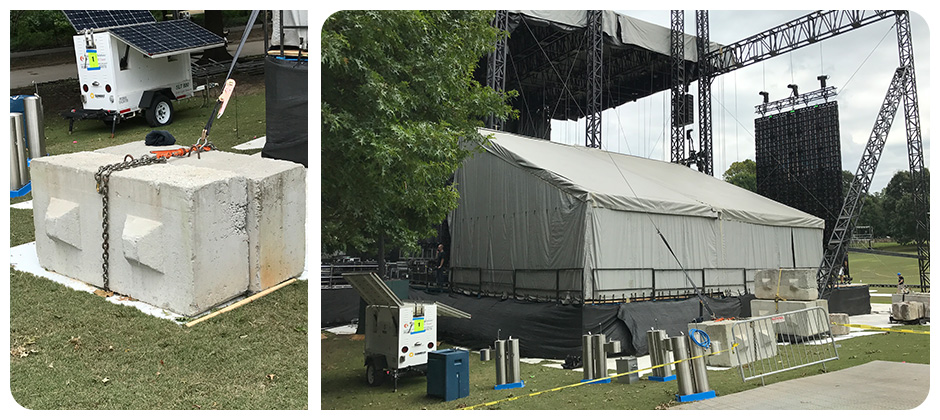
How to calculate ballast.
The vertical force of the wire rope wants to lift any ballast off the ground, and the horizontal force wants to move or slide it. Both must be accounted for and resisted by the ballast. The vertical force, or uplift, is fairly straightforward. Some portion of ballast must be equal in weight to the value of the vertical force. The weight required is multiplied by a desired factor of safety, as identified in the governing building code, and the design of ballast for uplift is complete. Basically, the ballast has to be as heavy as the uplift, plus a little more for added safety, typically 1.5 per code. If the force in the wire rope is 1000 pounds, providing just 1000 pounds of ballast is not a very good factor of safety against mother nature.
The design of the horizontal component is a bit more complicated, and is a function of the surface where the ballast rests. The weight of the ballast used to resist the vertical component cannot be counted on to resist the horizontal component, too. Adding weight to the ballast amount is the answer. The smaller the friction between the ballast and the ground surface, the more weight required to prevent sliding. This fall, when you’re playing backyard football, you can slide a lot easier on the grass than you can on the backyard patio. Now think about pushing a concrete block on grass instead of the patio. Wet ground makes it even easier to slide. Typical friction coefficients between concrete and wet dirt or grass, or the plywood placed underneath the ballast, range from 0.3 to 0.4. The horizontal force that ballast can resist is the weight of ballast multiplied by the coefficient of friction. Without considering a factor of safety, the weight of the ballast used to resist horizontal forces must be almost 3 times the horizontal force on these types of surfaces. This can lead to some sizeable ballast. The weight required to resist the horizontal force is multiplied by a desired factor of safety and added to the previously calculated ballast for uplift. In addition, the location of the wire rope on the ballast is critical. If for instance, you attach a wire rope to the top of a tall, thin element, the horizontal force could easily tip this ballast over. This is not an ideal situation.
In some instances, where failures of roof systems have occurred, the coefficients of friction between the ballast and ground surface have been too high. When an unconservative value for coefficient of friction is selected, or if the presence of moisture is not considered and the ground surface becomes slippery reducing the previously assumed coefficient of friction, the factor of safety is lost, and a serious wind event will move the ballast. When ballast is moved, the wire rope can lose tension or break in the opposite direction, resulting in a loss of stability for the roof system. If the wire tension becomes slack from sliding ballast, it allows the top of the stage to move more at the top. Even a couple of inches of lateral moment in a roof system that holds tens of thousands of pounds of rigging, 40 to 50 ft in the air, can dramatically increase stresses and forces in the roof system supports. When either occurs, the result can be catastrophic, leading to the collapse of the roof, stage or the entire structure.

Next time you’re at an outdoor show, watch the artist, but take a look at what’s keeping the roof in the air. Check out the wire ropes and straps attached to the ballast. Ballast might not be as appealing as the stage, or sound as elegant as the show, but safety and stability are paramount to your enjoyment of the event.
I’m planning to organize a small theater production that is a form of an adaptation and reinterpretation of a movie I saw when I was a kid, and it uses flying effects since all of the characters are flying in the movie. It’s fascinating to know that ballasts are responsible for anchoring everything seen at the stage so that everything’s stable. I think I’ll hire someone to create this effect for me since I’m not familiar with how roof systems work. http://theflyguy.com/videos
Thanks for the comment! We’ll reach out via email to discuss your project.
How much ballast do I need for a 20ft lighting tower? truss weight and lighting units (hung on top 10ft) totalling 900 lbs
Each installation is unique and should be reviewed for site constraints. We’ll reach out via email to understand your installation better.